Sponsored Feature: The making of the new Hyundai Santro
The car that launched Hyundai in India is back. We go behind the scenes to see how it all comes together.
Published On Jan 04, 2019 10:27:00 AM
9,601 Views
Follow us on
Early morning, December 2018. Sriperumbudur, Tamil Nadu. An articulated truck enters the Hyundai factory gates, its trailer straining under the weight of tonnes of cold-rolled steel coils. After passing through the mandatory security checks, it makes its way slowly to the oversized doors of the press shop. The cold-rolled steel coils are unloaded and this is the point where the new Hyundai Santro begins its life. From here to the end of the line in another building on the massive Hyundai factory premises a couple of days later, the transformation from simple blanks of steel to a car with its own identity takes place.
.jpg&c=0&w=700)
On the premises are two factories, each one sending out a brand-new car (new car smell included) once every 33 seconds. This kind of efficiency requires planning on the scale of a mission to Mars to ensure that quality is up and wastage is down, especially since the plant we are in today manufactures the Grand i10, Xcent, Verna and Santro on a single line and in no particular order other than the one that’s on the order books. Shall we get into it then?
.jpg&c=0&w=700)
Twenty years and counting
The name stays the same but the manufacturing processes have changed. After making close to 1.8 million old Santros for both the domestic and export market, the key differences from the new one (in terms of manufacturing) are mostly in more efficient processes and a big move towards automation.
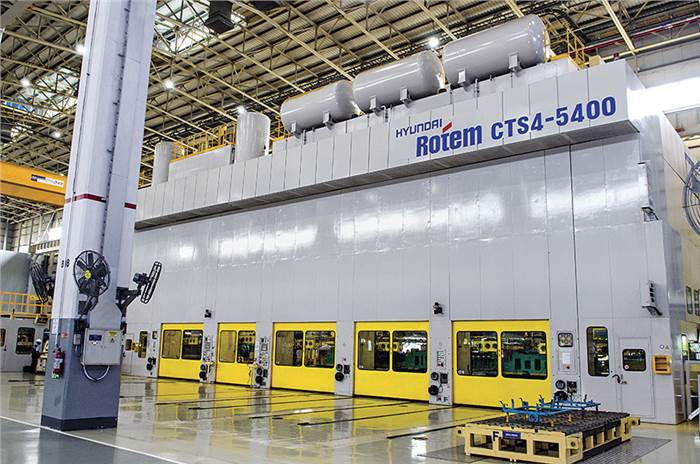
Hyundai has a digital pre-assembly system in place where they can virtually assemble a new model before the car is actually on the line. This helps them predict possible problems and also helps refine the manufacturing process to ensure no mistakes are made when the car is physically on the assembly line.
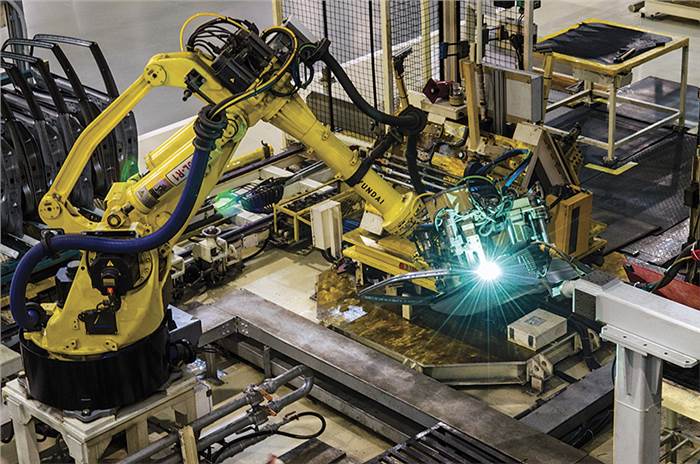
The other key difference in manufacturing is that the old Santro was made using human-intensive processes whereas a lot of software and robots are behind the assembly of the new one. The body shop and paint shop are completely digitally managed and mapped. Hyundai says they have moved from completely human-intensive processes to a human-digital partnership to now having some processes that are completely digital.
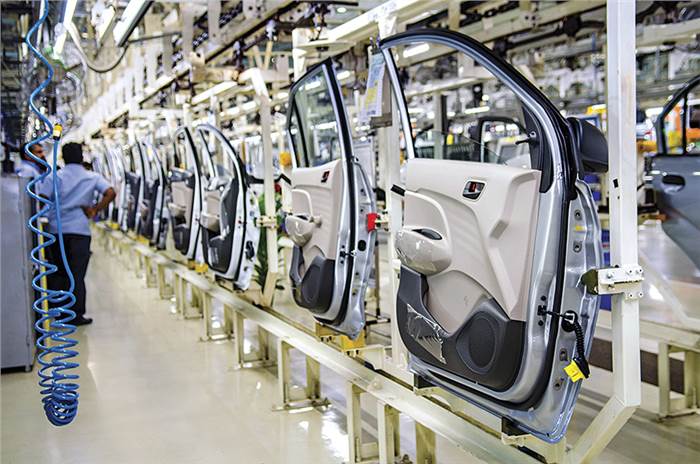
Hot off the press
Close to 63 percent of the new Santro’s body is made from high-strength steel, so once the cold-rolled steel is in the press shop, they are unrolled and converted into blanks. Blanks are sheets of steel that can be pressed into specific panel shapes. Raw steel is ordered only for the production plan for the day and once the blanks are made, they go into the press to be pressed into the shape of the panel that is required for production. Each one of the five presses in the press shop can exert up to 5,400 tonnes of pressure to get this job done. The press shop manager tells us that about 250 tonnes of steel passes through this shop every day. The dies in the press can stamp up to 1,000 steel sheets in one go before they are pulled out for inspection, and the same goes for the stamped sheets. A quality check officer pulls approximately one finished panel out of fifty to ensure the panel is up to standard. If a defect is found, the batch is recalled.
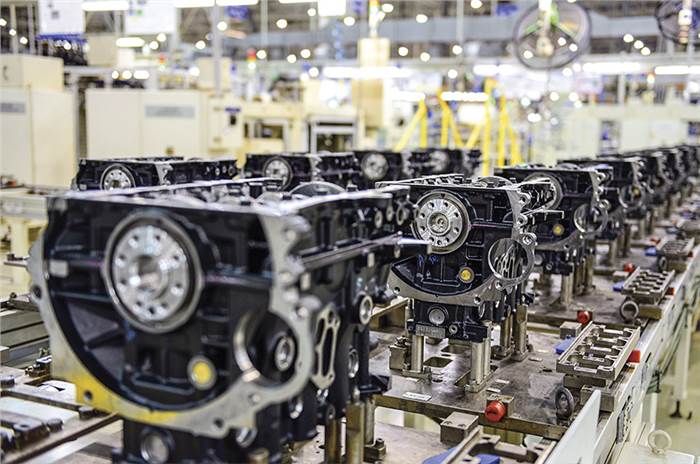
The manager is particularly proud of the built-in vibration analyser in the presses that measures every stroke of the press. If it detects even the smallest of strain, it stops the press to ensure corrections can be made in time.
.jpg&c=0&w=700)
Shapely figures
The freshly pressed panels then move to the body shop where more than 500 spot-welding robots get to work, assembling them into the shape of a car. Along the right side of the shop, the doors, hatch/boot lid and bonnet are welded and the line on the left constructs the monocoque chassis of the car. The robots are smart so once the panel is in place and the robotic arm moves into welding position, the sensors in the arm take a decision in microseconds about what kind of voltage needs to be passed through that particular point of welding, and passes it exactly through that spot. There is no human interaction here, to ensure that the body panels leave the shop flawlessly.
.jpg&c=0&w=700)
The colours of life
The finished bodies then move to the paint shop where every body goes though 3.5km of processes to ensure that it is corrosion-free for the rest of its life. Four coats of various paints get put on to the body here. First up is Electro Deposition (ED) coat that has become universal for the modern automotive paint shop. The ED coat is basically the body’s main weapon against corrosion. This is followed by a primer coat, an intermediate coat and finally the top coat. Again, all of this is done by robots – including the interior paint and underbody sealant – for the export as well as domestic market. The painting process is the single longest process in the making of a car. The body spends approximately two days in the paint shop, drying the different layers of paint before it is ready to take on the wiring and mechanical bits.
.jpg&c=0&w=700)
The oily bits
Next up is the engine and transmission. The 1.1-litre, four-cylinder engine in the Santro has been in the Hyundai stable for ages but the new automated manual transmission (AMT) is special. Hyundai says they are the only company in India that has developed and manufactured the AMT in-house. Seventy-four important processes have been implemented to make the AMT, and more than a few of these are to measure and keep quality checks on the assembly process and finished product. It measure the way it gets assembled and finished and also measures it for harshness and noise. Once all the checks are done, the finished engine and transmission move to the final stage of assembly.
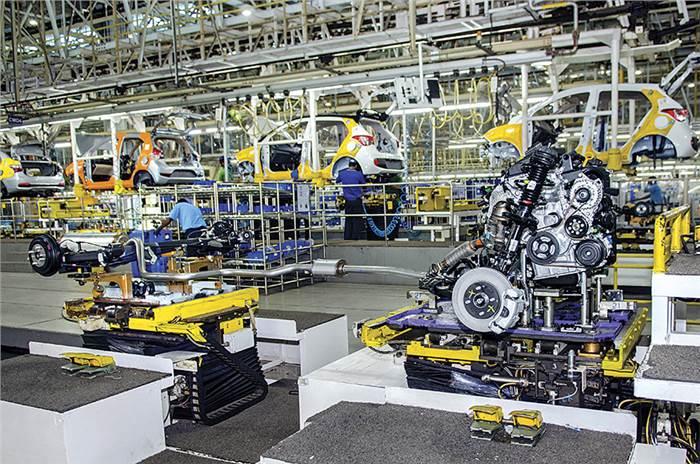
The marriage bureau
It all starts coming together at the assembly shop. Once the body enters this shop, the dashboard and some of the wiring are some of the first things to be fitted. The engine, suspension, brakes and exhaust arrive as a single module on a separate line and the body literally drops on to this module in a process they call ’chassis marriage’. Then, the manual intensive bit of the manufacturing process starts. As the car moves through the 200 varied stations in this shop, workers attach the doors, trim and equipment and the car finally starts taking the shape we see it when we go to a showroom. The workers are assisted digitally by way of visual controls and also information on the exact component that needs to be fitted and a digital inspection system ensures that all the parameters are in check.
.jpg&c=0&w=700)
The processes in the assembly shop also involve 5,000 quality checks to ensure that all the moving parts are absolutely as they should be.
The end of this line is where the new engine is started for the first time and the car moves off under its own power for a quick spin on the test track within the factory premises.
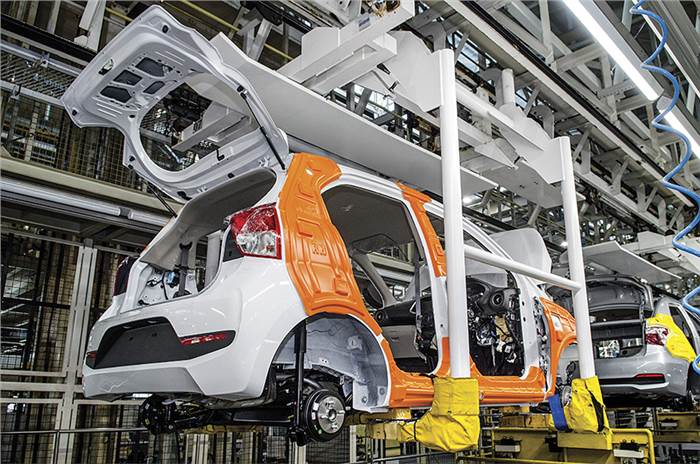
The final countdown
If everything is okay at the test-drive stage, the car moves to the pre-delivery inspection area, where it goes through 200 further quality checks and gets final touches like the addition of the tool kit and the owner’s manual. Small problems discovered at this stage are fixed on this line, whereas for bigger problems, the car is pulled off the line and sent to the concerned department for correction.
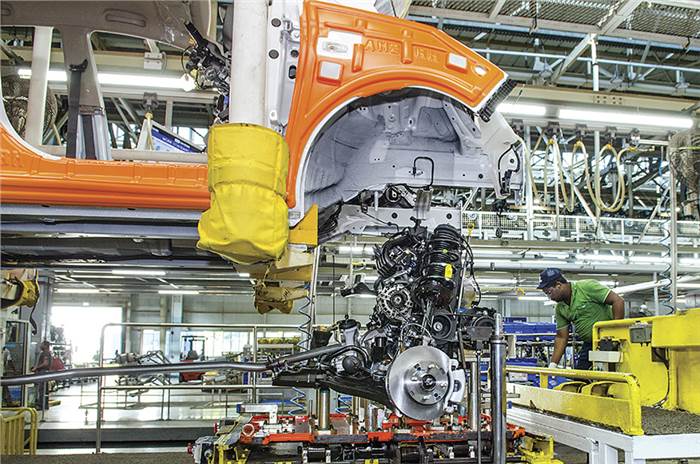
Finally, the finished car is sent to the massive parking lot in the factory where it awaits a new home.So, if you’ve ever wondered why Hyundais run so reliably, now you know.
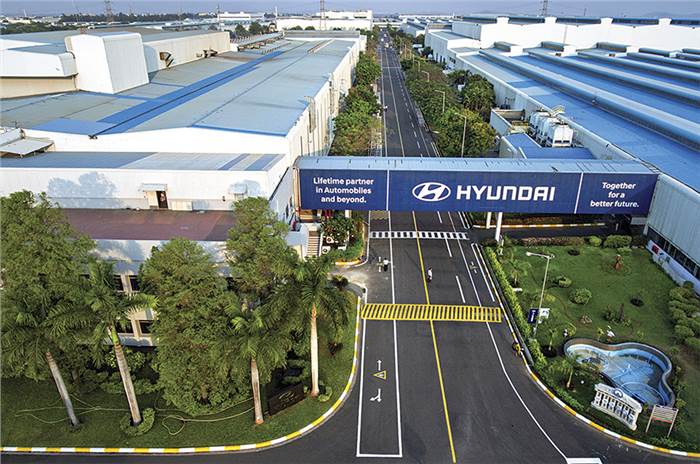
Copyright (c) Autocar India. All rights reserved.
Comments
Member Login
Personal Details
No comments yet. Be the first to comment.