Maruti Suzuki factory visit: Making of a Jimny
The Maruti Suzuki plant was set up back in 1983, but today, it’s home to the company’s most modern line.
Published On Feb 11, 2024 08:00:00 AM
17,594 Views
Follow us on
Standing in the passageway between the office complex and the factory floor at Maruti Suzuki’s Gurugram plant is like standing at the confluence of two eras. On one side, you have 1980s architecture and materials meeting futuristic robots, and on the other, automated vehicles.
I had visited the plant a number of times in my previous job, and I can swear I even recognised individual tables from back then. Even the wood panelling on the walls and the staircase banisters were all just as I remembered them from about 20 years before, and I’m pretty sure they were there 20 years prior too.
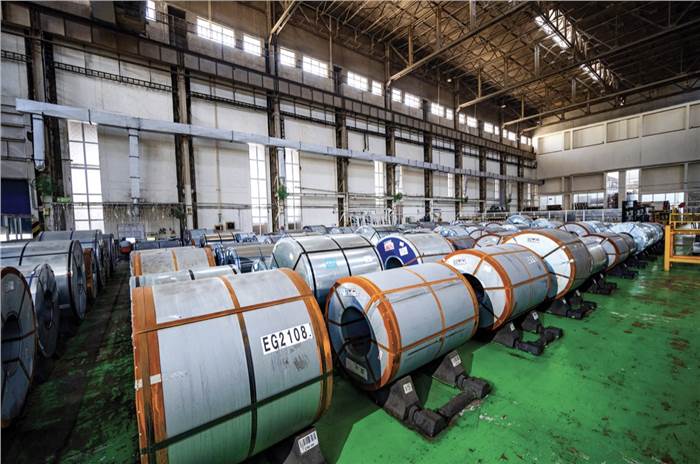
Yet, peek through the glass panes at the factory floor and it’s a completely different era. Robots welding and lifting, and autonomous vehicles transporting parts across the floor look very much like any other up-to-date modern factory. In fact, Maruti says that by virtue of this being the newest line they installed, it’s also the most modern one. Seeing this contrast between areas like the factory meeting rooms and the work floor was my highlight of the tour Maruti organised for the media.
The Gurugram plant was set up in 1983 and has a capacity of 5 lakh units per annum today. While it began making the Maruti 800, today it produces vehicles like the Ignis, Alto K10, Eeco, Super Carry and also the Jimny, and this is the line we got a guided tour of. Given the high level of localisation that Marutis have, this line begins with rolls of steel that are cut and then pressed into shape to form various body panels of the Jimny. The welding is nearly exclusively done by robots, which was nice given that this was a highly human-dependent operation when the plant started. Chassis welding too – the Jimny has a body-on-frame construction – is robotic.
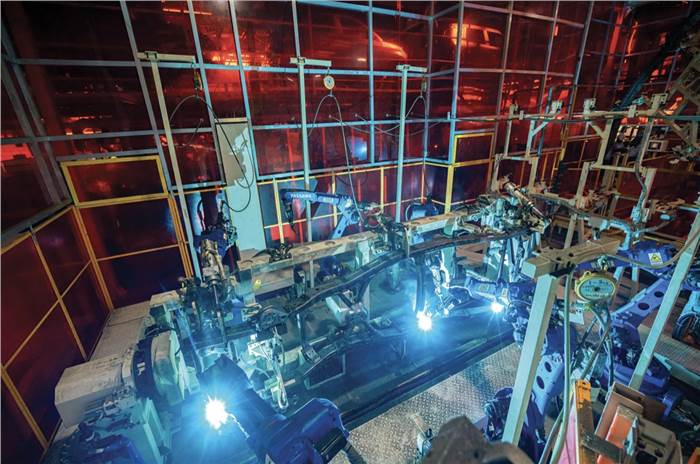
The body and chassis are joined together robotically and it is actually quite a sight to see – the body is lifted and put into place by a large, robotic arm onto the chassis, which itself is rolled into place by a fully autonomous electric trolley. The joining is only temporary for the paint shop, which, given the high level of dust-proofing, was off-limits on this tour. The body and chassis are then separated again for further assembly of components; the chassis gets the engine, gearbox and suspension, while the body is fitted with the assemblies like the dashboard. A lot of this work is done by humans but workers have rigs to help with heavy lifting.
What’s also neat is that depending on the individual height of the operator, the entire body and assembly is lifted and rotated into a position to avoid the person having to bend or twist to accomplish a task. Once both chassis and body assemblies are ready, they are finally joined together, and what now looks like a finished car proceeds down the line for smaller fitments, final inspection and testing. Here too, while the operation is done by skilled technicians, there’s new tech deployed. What impressed me was the wheel aligner that isn’t laser but an ultrasound unit, which the company says is better off than the laser light aligners.
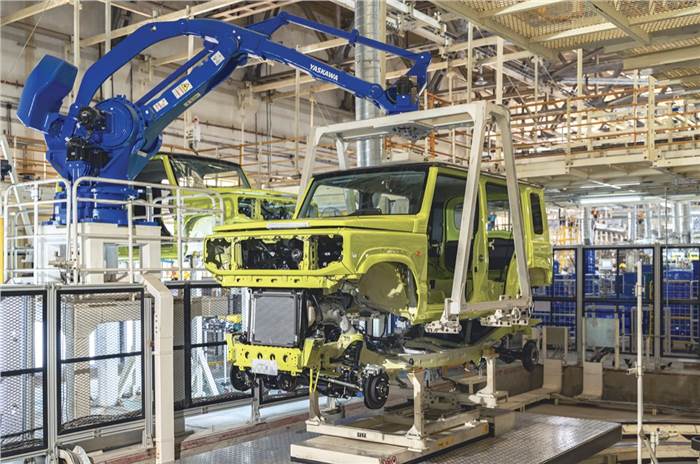
As with all things Japanese, the tour is quick and efficient, and we end with a reminder to not report anything beyond what was allowed. Though I have to say, there are some pretty neat colours that export markets get that we don’t. Check out the Australia and South Africa sites and if you like them, give Maruti a holler.
Factory Facts
What was once a floor teeming with workers is today a blend of humans and robots working as a team.
Spread over 300 acres
Located in Gurugram; 15km from Delhi International Airport
Employs 13,000 people
Runs 16 hours in two shifts
150 rain water harvesting wells and a lagoon with a capacity of around 49,800 kilolitres
Has a 5MW solar plant
Also see:
Maruti to launch Fronx hybrid in 2025
New Maruti Swift India production to start next month
Copyright (c) Autocar India. All rights reserved.
Comments
Member Login
Personal Details
No comments yet. Be the first to comment.